Roller compactors, in construction and infrastructure development, operating within a very fast-paced environment, are really the ones that keep things stable and durable, but the most surprising thing is that they do it silently, i.e. the roads, foundations, and landscapes.
Importance of Regular Roller Compactor Service
These heavy-duty machines are cost effective and their continuous, reliable performance is crucial to the success and profitability of the project. Though roller compactors are tough, they need the care of their owners because stopping their operation for more than a few hours is a severe loss of profit.
Just as any other machinery, roller compactors are being used constantly and are thus prone to heavy and serious wear and tear that is why they also need regular maintenance. The lack of their regular maintenance will result in various problems followed by a chain reaction leading to substantial financial loss.
Why this Blog?
This blog is going to show you which are the reasons for the regular maintenance of your roller compactor and why it is not just for safety but also it is a very important financial strategy which you may not even imagine how much it can save you.
The Financial and Other Losses If Regular Services Are Not Done
The majority of the equipment owners stitch depreciation as a pressing issue and then they believe that the roller compactor service is a kind of pointless expense which exactly shows the wrong approach. The reality is apart from costs that equipment owners need to deal with them are even higher if they react in a less coming time.
The problems which seem unimportant to be solved during regular maintenance will become very suddenly something which is in very bad condition, therefore it is required to enforce a replacement of some of the machine’s elements, which usually takes days meaning that the further development of the process be in danger. However, the real expenses of the unoperated machine could even cause the writing-off of the whole project, the labor input you had and do a backfire to your reputation.
1. Costs caused by augmentation:
A minor issue may require considerable resources if not solved from the very beginning. A damaged bearing that is not substituted immediately can lead to the total rupture of the vibratory drum assembly, a very high-cost repair. So, a small leak in the hydraulic system may turn into a huge one, and if not checked in time and this gets worse, it would ask for expensive repairs or even for the whole system to be replaced.
The disuse of regular fluid changes can provoke the pollution of the oil, which in its turn can bring about the wear and tear of the components of the engine and the hydraulics. Reacting this way to failures, that arise is much more expensive than the regularly applied and preventative maintenance.
2. Prolonged Downtime and Project Delays:
It is a disaster when a roller compactor goes out of order unexpectedly and the project is suspended. An idle machine for each hour is equivalent to productivity lost, postponement in project completion, and potential fines for defaulting on deadlines.
One machine failure can cause a chain reaction of a series of hitches in the workflow system and thereby other tools and workers on-site may also be affected. This downtime incurs direct financial losses and is capable of seriously discrediting the company.
3. Reduced Equipment Lifespan and Premature Replacement:
A roller compactor, which is properly maintained, has a good chance of serving your business well for a substantial number of years. On the contrary, a machine that is ill-treated will have a full scope of wear and tear, which will result in substantial shortening of the operation period.
This, in turn, obliges a company’s management to spend money on a new expensive roller compactor much earlier than planned, that is in order to double the capital cost. Regular maintenance is such a factor that it provides the reliability of all parts, thus extending the operational life of the machine and enhancing the rate of return for shareholders.
4. Compromised Performance and Quality of Work:
A faulty roller compactor is very limited in terms of capacity. Examples of some causes of failure resulting in worn drums, dysfunctional vibration systems, or incorrectly fitted parts are non-uniformness in compaction, uneven surfaces, or poor finishing.
This situation not only poses a threat to the work quality but can also lead to expensive reworks, customer dissatisfaction, and even legal disputes. Always retain the peak performance of the compactor to ensure that your quality stands out on every occasion.
The Unseen Savings: How Roller Compactor Service Returns Money to Your Pocket
Although it may look like a senseless action to spend money on something that is not apparently broken, the regular roller compactor servicing brings the economic benefits in the long term, which are irrefutable. It is a kind of investment that will not only ensure you the normal operation of the machine but also the longer life of your asset. Besides, you will also avoid those costly failures.
1. Preventative Maintenance Prevents Costly Breakdowns:
The key principle in regular servicing is proactive problem-solving. Identification and timely elimination of small problems will help you avoid the major breakdowns and the corresponding expensive repairs. The maintenance includes scheduled checks, replacement of liquids, filters, and lubrication of machine parts. Think of this as your machine’s regular health testing – finding possible problems before they worsen.
2. Optimized Fuel Efficiency and Reduced Operating Costs:
A well-adjusted and checked engine, a replaced air filter, and the moving parts that are adequately greased are the key to your machine’s consistent peak performance. Through this, not only you directly contribute to the reduction of the fuel consumption, but also you realize the significant savings from its entire lifespan, especially when considering that fuel prices are always in fluctuation. Moreover, a minimal wear and tear due to the efficient operation do not necessitate the frequent change of parts thus reducing even the maintenance cost.
3. Extended Equipment Lifespan and Higher Resale Value:
Regular servicing is the most effective way to extend the life of the compactor. With the following of the recommendations made by the manufacturer concerning maintenance constantly, you end up aggregating the least possible wear and tear on the vital components and, by so doing, they become long-lasting. When the time for the upgrade comes, the well-maintained device will bring a lot of money back and also, a subject of a higher resale value.
4. Enhanced Safety for Operators and Crew:
Any equipment stopping to function properly is equal to an industrial disaster that can cause any operator and someone working beside the area to be at the serious risk. A regular check-up makes certain that all means of safety are functioning, hydraulic systems are healthy, brakes are reactive, and all the components are moving as planned. This always on-alert method is effective in reducing the case of an accident, that is, by taking place of the personnel, and also, the legal liability for the company.
What Are the Features of Regular Roller Compactor Servicing?
Regular roller compactor service is usually performed through a predefined set of checks, inspections, and preventive measures, which are all adjusted to the specificity of the machine, its age, and operational hours. Typically, a complete servicing plan will consist of the following:
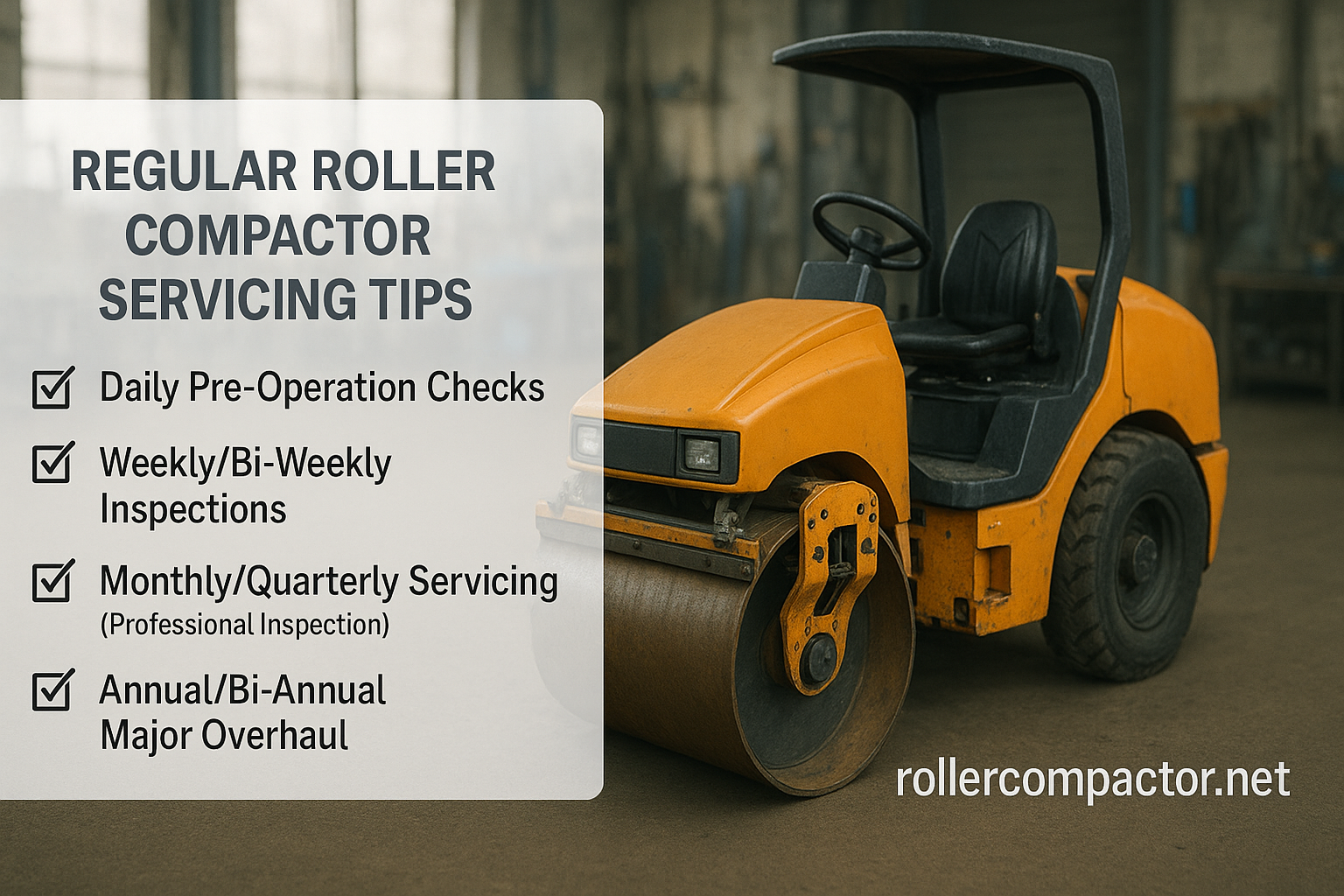
Daily Pre-Operation Checks: Such inspections are those which the operator carries out before each working day. It may be simple checks done in a visual manner, but they are usually the first indicator that tells of an immediate issue that has to be addressed as soon as possible.
- Monitoring the fluid levels (Engine oil, hydraulic fluid, coolant, fuel).
- Looking for damage, wear, and making sure that tires/drums are of the right size and properly inflated.
- Seeing if there are oil, hydraulic fluid, or coolant leaks.
- Testing all lights, alarms, and safety features if they are all in good working condition.
Weekly/Bi-Weekly Inspections: More complex checks that extend further than just following the daily routine.
- Regular lubing of all recommended grease points according to the manufacturer’s advice.
- Checking the condition and tension of belts and hoses.
- Examining the vapor system of the machine to see if anything was blocked and that it worked well for a jet of water.
- The removal of dirt from the radiator and cooling fins.
Monthly/Quarterly Servicing (Professional Inspection):
According to the schedule, this service is for complex and extensive checkups and the replacement of parts that are carried out by the technician.
- Replacing air and fuel filters.
- Observing the vibratory system to see if there’s any indication of wear and damage.
- Verifying the battery system for the absence of any slack connections or if the wires are broken.
- A very thorough exam of the braking system and steering components.
Annual/Bi-Annual Major Overhaul: This is a thorough check-up of the existing parts and their replacement.
- Performing an oil and hydraulic fluid change for the engine.
- New filters for all sections (oil, fuel, air, hydraulic).
- The whole system of the engine, gearbox, and hydraulic pump is up for inspection.
- Adjustment of the control systems and the subsequent functionality tests.
Preventative Maintenance by Application of the Investment Return Method (ROI)
Solid waste disposal and recycling operations management are in a position where a return on preparedness can be demonstrated. An expense of a few dollars periodically thus avoids the need for maintenance that costs several times more.
FAQs
Why is regular roller compactor servicing important?
Regular maintenance prevents the biggest breakdowns, cuts the expenses for repairs and prolongs the life of the machine, and, consequently, the user’s savings can go even to thousands of dollars over the years.
How often should I service my roller compactor?
It is commonly every 250-500 operating hours or as indicated by the manufacturer’s manual.
What are the key components checked during servicing?
In general, engine, hydraulic system, vibration system, drum wear, filters, and fluid levels are confirmed as well as the items to be replaced, if necessary.
Can delayed maintenance increase operating costs?
Yes, overlooked service tasks can result in fuel waste, malfunctions of parts, and they can also bring about expensive and long-lasting interruptions.
Does regular roller compactor service improve resale value?
$60% of the total costs are recovered by selling an equipment with a full history rather than a trained and experienced one, as the future buyers are willing to offer more for it.
How does preventative maintenance reduce repair bills?
On the one hand, it helps technicians to detect problems early and deal with them before they turn into major ones and on the other hand, it stops the possible hazards, which might increase the repair bills..
Are there digital tools to track roller compactor maintenance?
Yes, a lot of modern day compactors are equipped with telematics or fleet management software to manage, schedule, and have a detailed log of the maintenance process. The software is not only there to track when the equipment has had maintenance, but it can also efficiently manage inventory, and create reports for management.