Importance of Roller Compactor Spare Parts:
If you are a roller compactor owner or operator, you are well aware of the importance of keeping your roller compactor spinning and productive at all times. A single breakdown can stop a whole compaction operation, wasting your effort, causing you to lose money and time. Therefore, everyone needs to be sure that some parts are kept in stock as these are not only a recommendation but a must.
The article is a fully comprehensive manual, covering all aspects of roller compactors spare parts. Either your job is limited to one machine or you are in charge of a whole unit, saving a set of these spare parts will not only mean a paramount decrease in downtime, but it will also brighten the day in terms of efficiency.
The Necessary Inventory Preparation of the Rollers Operators Spare Parts
When you have the right item always ready, it means you are prepared for any sudden damage, common wear-off occasions, or routine maintenance. Here is why:
- Reduces Downtime: Waiting for parts to arrive can be a thing of the past, and you get back to operation quickly.
- Saves Money: Getting something sent overnight or quickly delivered can be very costly.
- Improves Machine Life: The key is to change any old components right away to shield the other parts.
- Boosts Efficiency: Without unnecessary stops, a team operates and thus the work would flow faster at the job site.
List of the Essential Roller Compactor Spare Parts
Checkout the list of the essential roller compactor parts listed below:
1. Vibratory System Components
What is a vibratory system of a roller compactor?
The vibratory system is a roller compactor’s primary part and usually represents its core. Such a part assists in soil and asphalt compaction by transmitting the necessary vibration.
Spare Parts to Verify:
- Parts that are Excentric Weight and Shafts: They can be the first to fall out of use because of the turn of a new engine.
- Hydraulic Vibrator Motors: The progress of constant heating and operations weakens their functions.
- Vibration Bearings: These must be changed regularly to avoid any further injury to the vibration housing.
- Vibration Isolators/Mounts: It is the task of the mounts to absorb a sudden movement and protect the roller and the driver.
Such components give confidence to the owners that the vibratory roller compactors don’t stop working.
2. Engine & Powertrain Parts
So, unless the power unit and other parts of the drive are working smoothly, the roller is nothing more than a bulky mass of metal.
Do you have to have Engine Spares?
- Filters for Air, Fuel, and Oil: Help to remove impurities, add life to the engine, and increase mileage.
- A starter Motor and an Alternator: Connection and disconnection every time consume the motor and make the components wear out quickly.
- Drive Belts & Hoses: A common reason for this is excessive heat and friction, which may lead to splitting.
The malfunctions that can occur in the Fuel Injection System Components may even go as far as to lock the roller up.
Part | Purpose | Lifespan Estimate |
Air Filter | Filters dust from intake | 250-500 hrs |
Engine Belt | Transfers engine torque | 1 year or 1000 hrs |
Starter Motor | Starts engine ignition | 2-3 years |
Fuel Injector Nozzle | Ensures proper fuel atomization |
3. Maintain Hydraulic System Properly
Roller compactors have hydraulic systems for guidance, vibration, and motion. In the presence of these systems’ faults, the machine can be rendered immovable.
Hydraulic Features that Are Indispensable:
- Hydraulic Pumps: To be replaced in a preventive manner based on usage.
- Control Valves & Cylinders: They are steering and lifting essentials.
- Hydraulic Hoses & Seals: Their common failure results from both wear and pressure surges.
- Fluid Filters & Reservoir Caps: These elements are responsible for keeping the system clean and hermetic.
In hydraulic systems, pollution is the major cause of their death. Clean filters = a long life of the part.
4. Drum & Roller-Related Parts
The compaction drum is where the work gets done. Drum wear or imbalance can compromise compaction quality.
Parts You Should Stock:
- Drum Scrapers & Cleaner Blades: Regularly remove scrapers and cleaner blades for the drum and avoid the accumulation of debris.
- Drum Bearings: Keep the barrel rotating and tolerate heavy loads causing the rotation of the barrel.
- Drum Shell Segments: They are capable of being broken if they are under the high load, or if it is a bad case.
- Water Spray Nozzles & Pumps (for asphalt rollers): To substratum of the rollers stick the hot asphalt.
5. Electrical and Control Components
Drum and Water Spray Nozzle Pump are a direct example of that.
Electrical Spares Worth Stocking:
- Fuses & Relays: cheap, critical, and usually the first to fail apart.
- Control Panel Switches & Displays: No more malfunction due to vibrations.
- Sensor Units (Speed, Temp, Pressure): Necessary for the performance of the machine.
- Battery Terminals & Harnesses: The problems associated with batteries are one of the root causes of the faults.
Use a complete stock of electrical kit to avoid unexpected power loss.
6. Tires, Rims & Undercarriage Parts
Hard hats are essential for the safety and protection of the operator.
Recommended Spares:
- Tires & Tubes: Keep 1–2 spares to avoid long waits.
- Wheel Bearings: A part of regular maintenance.
- Bolts & Fasteners: Stock tire bolts, wheel nuts, and axle bolts.
- Rim Flanges & Lock Rings: Terrain impact is a major cause of the damage.
7. Operator Cabin & Safety Gear
Even if the operator’s cabin is not a mechanical part of the machine, it is still a must-have for safety and regulation purposes.
Some of the Safety Components to Keep On-Hand:
- Seatbelts & Mounts
- Backup Alarms & Lights
- Mirrors & Wiper Blades
- Cabin Air Filters
These parts have a beneficial impact on operator comfort, visibility, and regulatory compliance.
8. Consumables & Fasteners
Quite often, consuming the easy-to-find items is the answer; the critical thing is to replenish and keep them in stock.
Stock Up On:
- Grease & Lubricants
- Loctite, Anti-Seize Pastes
- Nuts, Bolts, Washers
- Seal Kits & O-Rings
Create a labelled, well-arranged consumables rack for convenient retrieval.
Sample Roller Compactor Spare Parts Checklist Table
Category | Spare Parts | Criticality | Stock Qty |
Vibratory System | Eccentric shaft, vibrator motor, mounts | High | 2 each |
Engine & Powertrain | Filters, belts, starter motor, alternator | High | Varies |
Hydraulic System | Seals, hoses, fluid filter, pump | High | 3 each |
Drums & Rollers | Scrapers, bearings, shell segments | Medium | As needed |
Electrical | Fuses, sensors, control switches | Medium | Pack of 10 |
Tires & Undercarriage | Tire set, bearings, bolts | High | 1 set |
Safety Components | Seatbelt, alarm, wipers | Low | 1 each |
Consumables | Grease, nuts, Loctite, O-rings | High | Monthly Refill |
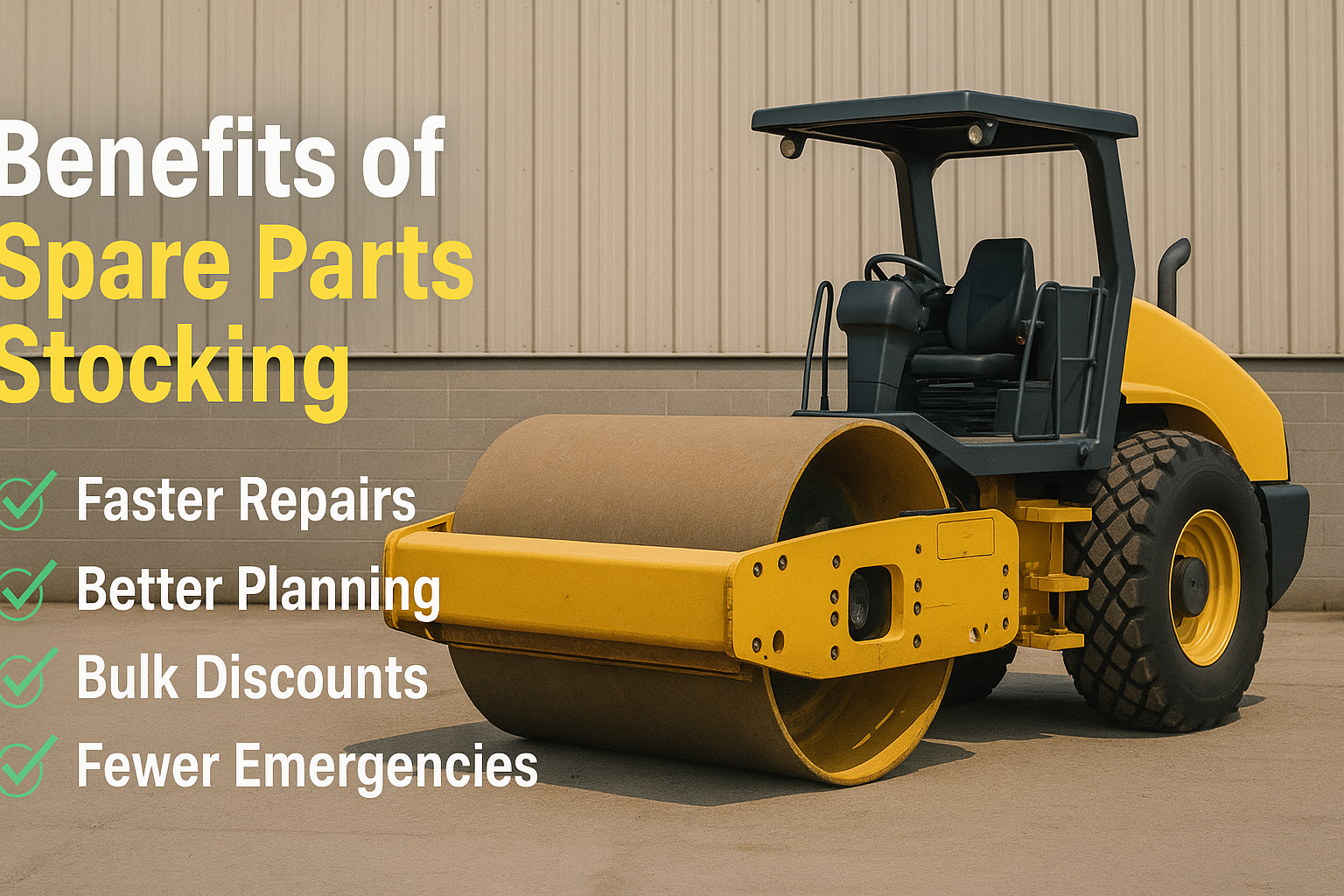
Benefits of Preventive Stocking
Stocking roller compactor spare parts proactively is like having insurance for your roller compactor. The benefits include:
- Faster Repairs: On-site maintenance can start immediately.
- Better Planning: Budgeting for parts is more predictable.
- Bulk Discounts: Buying in quantity reduces cost per unit.
- Fewer Emergencies: Predictive maintenance replaces reactive chaos.
Tips to Maintain Your Spare Parts Inventory
- Use Inventory Management Software: Ensure to track stock levels and automate reorders.
- Label and Organize: Organize according to the shelves, bins, and QR codes help streamline retrieval.
- Rotate Stock: Always use older items first to prevent aging or expiry.
- Train Your Team: Ensure all operators and technicians underwent inventory training to know the inventory layout.
Final Thoughts
Your roller compactor is a high-powered machine that shouldn’t be taken for granted and needs extra attention. By stockpiling the necessary roller compactor spare parts for your inventory and ensuring that they are well maintained, you can still manage whatever problem comes your way—be it degradation or malfunction out of the blue.
The downtime is not something to wait for to understand that some parts are missing in the spare parts storage, and the message clearly says that you should be the one to initiate the situation, think ahead, and make your inventory the first step in your operational safety.
Additionally, Are you looking to get premium roller compactor parts?
If yes, then, we would be very glad to have you as our future client. We are rollercompactor.net
Frequently Asked Questions (FAQs)
- How often should I inspect my roller compactor spare parts inventory?
Monthly inspections are ideal for roller compactors. These high-use components should be checked weekly or after every major job performed to record its stability.
- What is the average lifespan of vibratory components like eccentric shafts or bearings?
Typically, the average lift span of vibratory components may range from 1000–1,500 hours depending on usage intensity. Always replace when vibration weakens or noise increases.
- Can aftermarket spare parts work as well as OEM parts?
In majority cases, yes—especially when the OEM products are brought from reputable suppliers. However, ensure compatibility and verify quality standards.
- Should I keep spare drums in stock?
It is impractical to keep spare drums in stock due to the high cost and the large amount of space required, but keeping drum shell segments or scrapers is suggested for emergency requirements.
- How do I prevent hydraulic leaks in compactors?
Hydraulic leaks in compactors can be prevented by regularly replacing seals, using quality hoses, and avoiding the system from being exposed to overpressure. Fluid cleaning process is essential to avoid any damages.
- Are software or electronic diagnostics needed for newer rollers?
Yes, software or electronic diagnostics are required to erase fault codes, and they can also use these tools to reset sensors. To secure these, try to keep them in an accessible place.
- What’s the best way to store hydraulic and electrical spares?
Always store hydraulic and electrical spares In dry, well-marked containers where there is no chance of mishaps to occur. For metals, use anti-corrosion bags and for electronics, store them in static-free boxes.