Soil compaction is a critical process in construction and civil engineering, significantly enhancing the load-bearing capacity and stability of the soil. The use of appropriate soil compaction equipment is essential to achieve the desired soil density and strength. Different types of rollers and compaction equipment are available, each suited to specific soil types and moisture conditions. This comprehensive guide delves into the various soil compaction machines, their classifications, and their applications, following Google NLP methods for SEO optimization.
Types of Soil Compaction Equipment
Soil compaction equipment can be broadly classified into two main categories:
- Light Soil Compacting Equipment
- Heavy Soil Compacting Equipment
1. Light Soil Compacting Equipment
Light soil compacting equipment is typically used for small areas where minimal compaction effort is required. These machines are essential for projects that involve compacting soil in confined spaces or for minor construction tasks. Here are the common types of light soil compaction equipment:
(i) Rammers
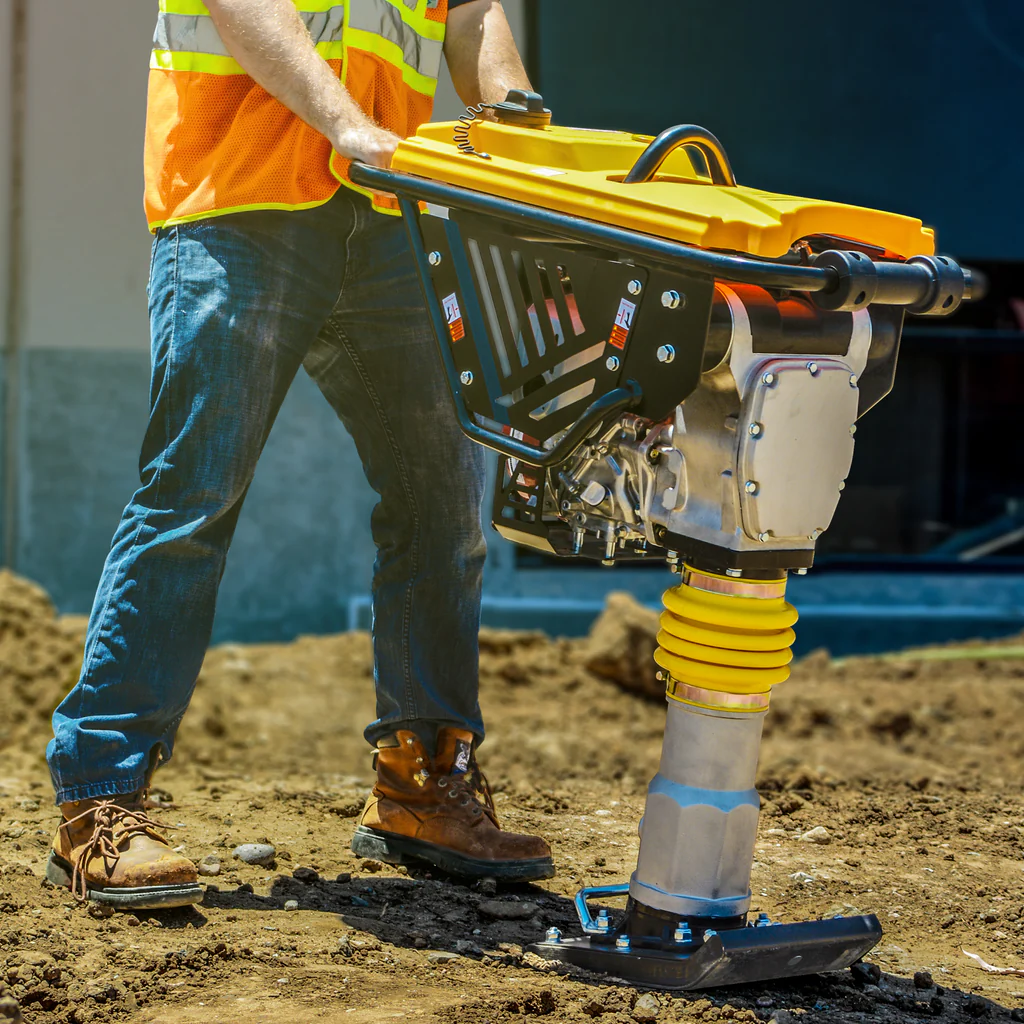
Rammers are designed to provide impact loads to compact small areas. They can be either hand-operated or machine-operated. Hand-operated rammers are lightweight and portable, making them ideal for tight spaces and small projects. Machine-operated rammers, on the other hand, can weigh between 30 kg to 10 tonnes. These machines are particularly effective for compacting cohesive soils and areas with difficult access.
The base sizes of rammers typically range from 15 cm x 15 cm to 20 cm x 20 cm. For machine-operated rammers, the usual weights vary from 30 kg to 10 tonnes. Rammers weighing between 2 and 3 tonnes are often allowed to free-fall from a height of 1 to 2 meters, delivering substantial compaction energy to the soil. These machines are highly effective for compacting cohesive soils and other soil types in confined spaces.
(ii) Vibrating Plate Compactors
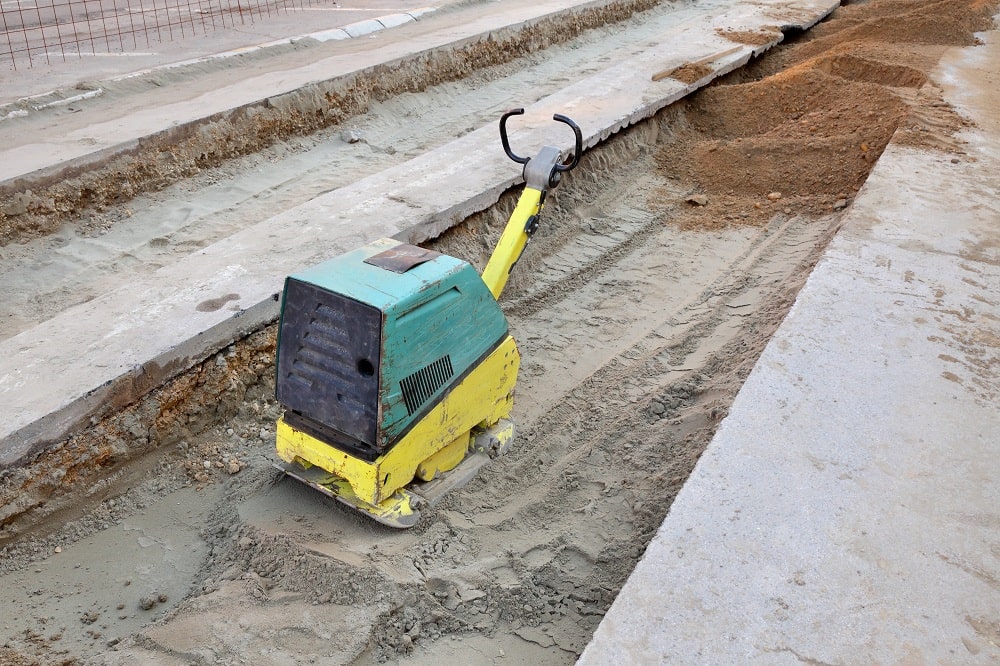
Vibrating plate compactors are ideal for compacting coarse soils with 4 to 8% fines. These machines are versatile and commonly used in small areas. They work by generating vibrations through a base plate that transfers energy to the soil, causing the soil particles to rearrange and settle into a denser configuration.
The typical weights of vibrating plate compactors range from 100 kg to 2 tonnes, with plate areas between 0.16 m² and 1.6 m². These compactors are effective in confined spaces and can handle various soil types, making them a popular choice for landscaping, road repairs, and other small-scale projects.
(iii) Vibro Tampers
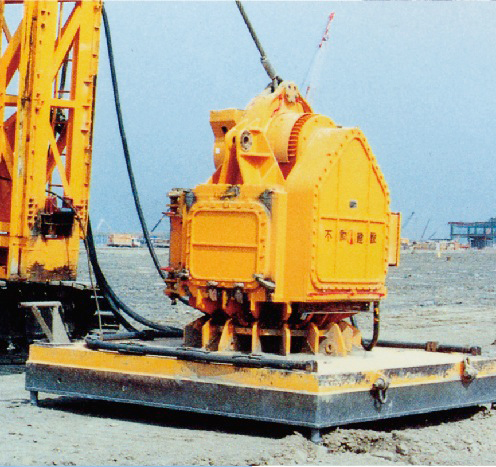
Vibro tampers are used for compacting small areas, especially in confined spaces. Due to the vibrations produced by an engine-driven spring-activated mechanism, these machines are suitable for all types of soil. Vibro tampers are manually guided and typically weigh between 50 kg and 100 kg.
The primary advantage of vibro tampers is their ability to deliver consistent compaction through vibratory action. This makes them ideal for compacting soils in trenches, around foundations, and in other restricted areas where larger equipment cannot operate effectively.
Learn More: Comparing the Performance of Vibratory vs. Static Roller Compactors
2. Heavy Soil Compaction Equipment
Heavy soil compaction equipment is designed for larger areas and more intensive compaction tasks. These machines are selected based on the type of soil and its moisture content. Heavy compaction equipment is essential for major construction projects, such as road construction, embankment formation, and large-scale landscaping. Here are the different types of heavy soil compaction equipment:
(i) Smooth Wheeled Rollers
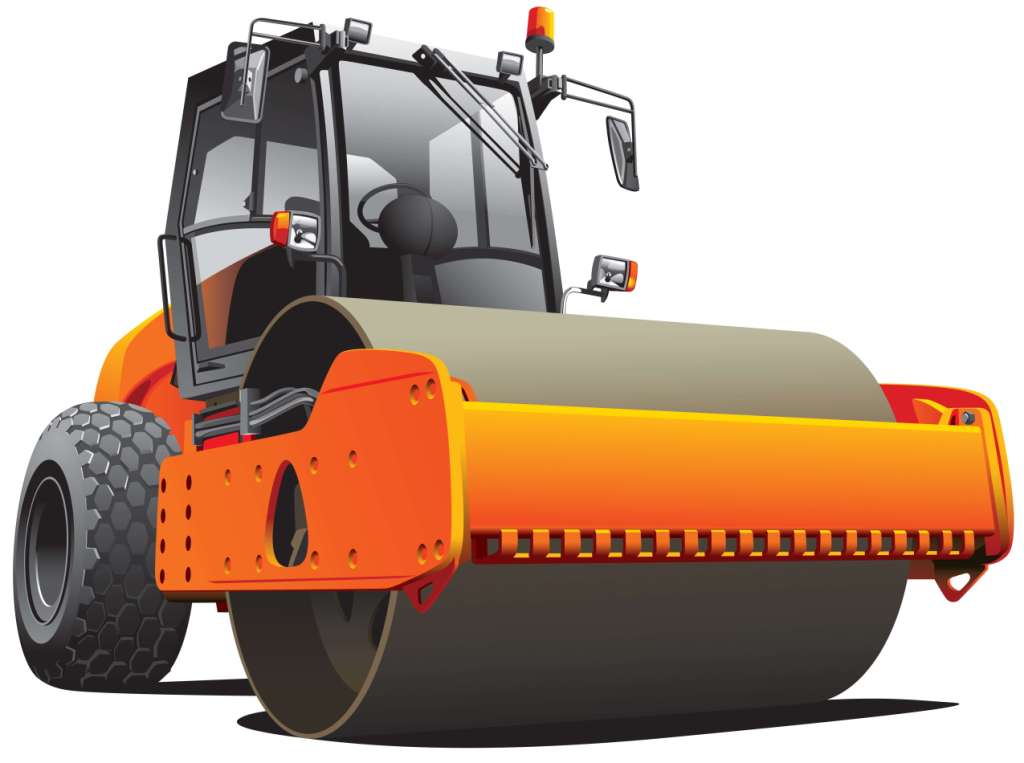
Smooth wheeled rollers come in two main types:
- Static Smooth Wheeled Rollers
- Vibrating Smooth Wheeled Rollers
Static Smooth Wheeled Rollers:
These rollers are primarily used for compacting well-graded sand, gravel, crushed rock, and asphalt. They consist of one large steel drum in the front and two steel drums at the rear. The gross weight of these rollers ranges from 8 to 10 tonnes. Tandem rollers, a variant of smooth wheeled rollers, weigh between 6 to 8 tonnes.
Static smooth wheeled rollers are effective for finishing the upper surface of the soil and are not suitable for uniform sands. The performance of these rollers depends on the load per centimeter width they transfer to the soil and the diameter of the drum. The load can be increased by ballasting the drum with wet sand or water, or by adding steel sections to the frame attached to the axle.
Vibrating Smooth Wheeled Rollers:
Vibrating smooth wheeled rollers employ rotating or reciprocating masses to generate vibrations. These vibrations enhance compaction by rearranging soil particles more effectively. Vibrating rollers can achieve higher compaction levels, compact soil to greater depths, and deliver superior performance compared to static rollers.
Although more expensive initially, vibrating smooth wheeled rollers are cost-effective in the long run due to their higher output and improved compaction efficiency. They are particularly recommended for modern excavation projects due to their advantages over static rollers.
(ii) Sheepsfoot Rollers
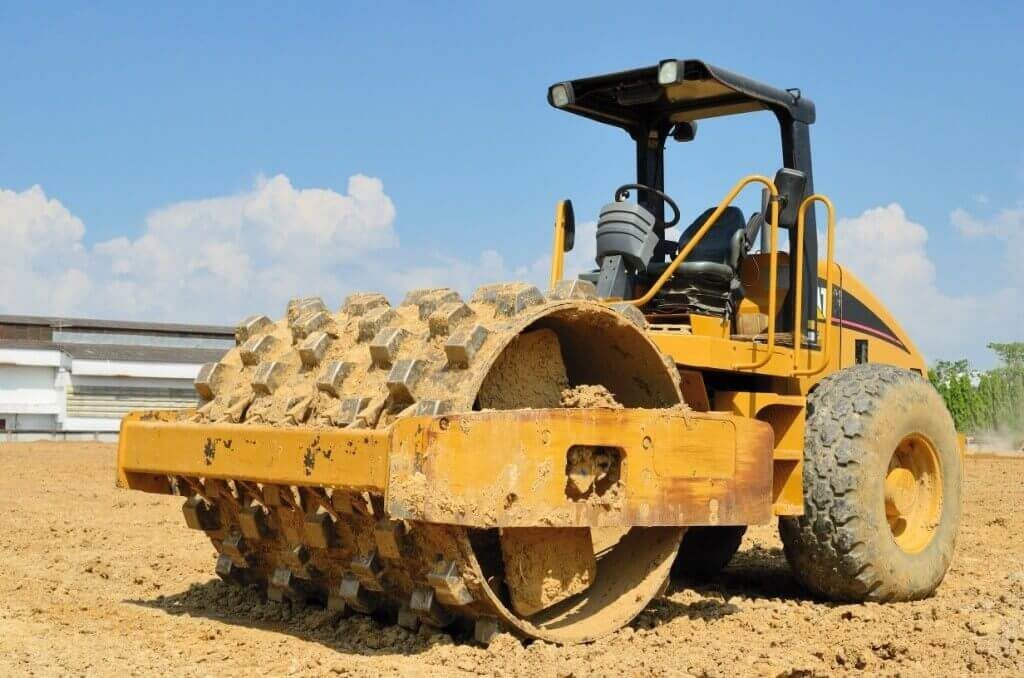
Sheepsfoot rollers are used for compacting fine-grained soils such as heavy clays and silty clays. These rollers are commonly employed in the construction of dams, embankments, subgrade layers in pavements, and railroad construction projects. Sheepsfoot rollers come in static and vibratory types.
Static Sheepsfoot Rollers:
These rollers feature steel drums with projecting lugs that apply pressure to the soil, causing compaction through kneading action. The pressure exerted can reach up to 14 kg/cm². The effectiveness of static sheepsfoot rollers depends on the weight of the drum, the area of each foot, and the number of lugs in contact with the ground at any time.
Vibratory Sheepsfoot Rollers:
These rollers combine the kneading action of the lugs with vibratory action, making them suitable for compacting all fine-grained soils and soils with sand-gravel mixes. The vibratory action enhances compaction efficiency and is particularly useful for subgrade layers in road and rail projects.
(iii) Pneumatic Tyred Rollers
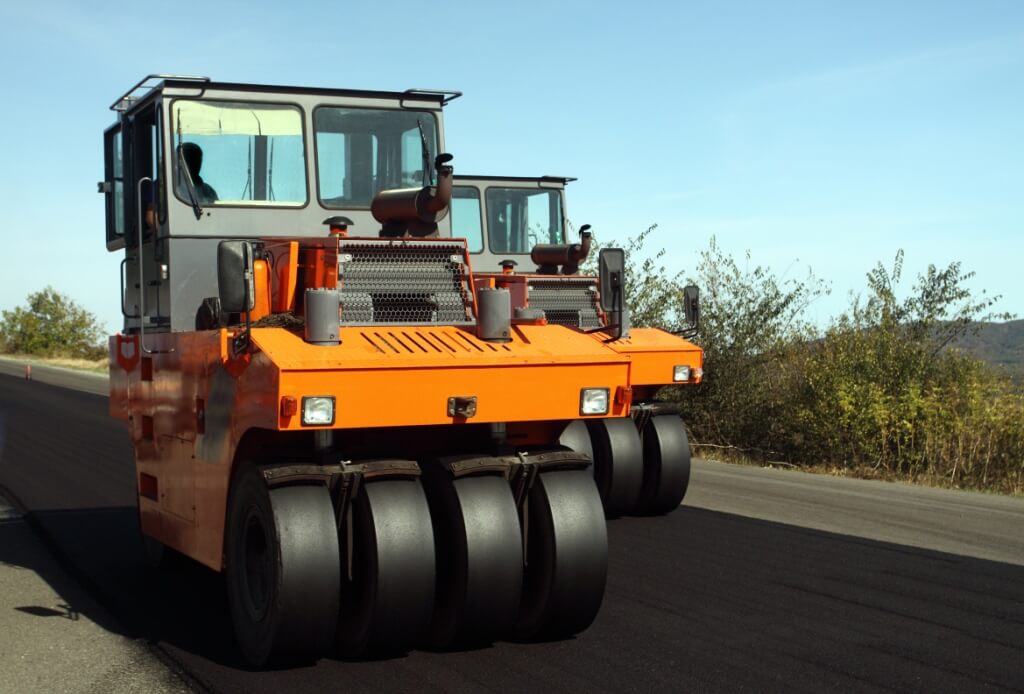
Pneumatic tyred rollers, also known as rubber-tyred rollers, are used for compacting coarse-grained soils with some fines. These rollers feature wheels on both axles, staggered to apply uniform pressure across the soil surface. Pneumatic tyred rollers are least suitable for uniform coarse soils and rocks but are highly effective for pavement subgrade works.
The degree of compaction achieved with pneumatic tyred rollers depends on the tyre inflation pressure and the contact area. Modern rollers come with an automatic tyre inflation system that adjusts the pressure as needed. The total weight of these rollers can range from 11 tonnes to 25 tonnes, adjustable by ballasting with steel sections or other means.
(iv) Grid Rollers
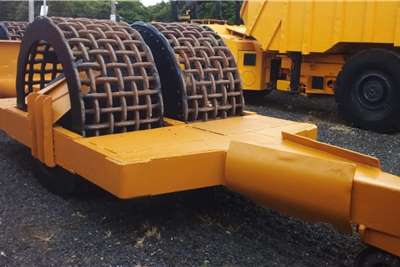
Grid rollers are designed for compacting weathered rocks and well-graded coarse soils. They feature a cylindrical steel surface with a grid pattern, providing high contact pressure but minimal kneading action. Grid rollers are not suitable for compacting clayey and silty soils.
Typical weights of grid rollers vary between 5.5 tonnes and 15 tonnes, depending on ballasting with concrete blocks. These rollers are primarily used for subgrade and sub-base compaction in road construction projects. The grid pattern ensures efficient compaction of coarse-grained soils by breaking down larger particles and achieving a uniform soil density.
(v) Pad Foot / Tamping Rollers
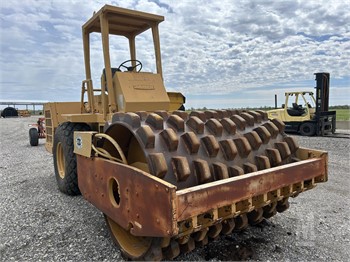
Pad foot rollers, also known as tamping rollers, are similar to sheepsfoot rollers but feature larger lugs. These rollers are highly effective for compacting cohesive soils and achieving uniform soil density. The static weights of pad foot rollers range from 15 to 40 tonnes, with static linear drum loads between 30 and 80 kg/cm.
Pad foot rollers are preferred over sheepsfoot rollers due to their higher production capacity and ability to operate at high speeds. They can break large lumps and spread material evenly, thanks to the leveling blades attached to the roller. These rollers are ideal for compacting cohesive soils in large construction projects, such as dam construction and embankment formation.
Learn More: Roller Compactor Safety Features and Certifications
Conclusion
Selecting the right soil compaction equipment is essential for ensuring soil stability and load-bearing capacity in construction projects. Light soil compaction equipment, such as rammers, vibrating plate compactors, and vibro tampers, is ideal for small areas and confined spaces. Heavy soil compaction equipment, including smooth wheeled rollers, sheepsfoot rollers, pneumatic tyred rollers, grid rollers, and pad foot rollers, is designed for large-scale projects and more intensive compaction tasks.
Understanding the specific applications and advantages of each type of compaction equipment allows construction professionals to achieve optimal compaction results tailored to various soil types and conditions. By utilizing the appropriate equipment, construction projects can benefit from enhanced soil stability, improved load-bearing capacity, and long-term durability.